Page 1 of 4
R1100S Fork Feet/Bottoms
Posted: Fri Sep 12, 2014 10:19 am
by Blinky
Hi Team Boxertrix,
I'm new here and am seeking some advice. I have a 1998 R1100S that I have been progressively tweaking and I am looking at a radial caliper fork conversion to mount 108mm pitch calipers (as a point of difference more so than a necessary mod).
I'm after some advice on how the existing fork bottoms/feet are fixed to the lower fork tubes. Given there's a grub screw through the inner side of the fork foot I'm thinking they may be threaded onto the lower tube and perhaps a Loctite style thread locker used. The grub screw stops rotation until the axle and wheel are assembled? Alternatively they may be a shrink fit.
If anyone has pulled them apart before or can throw any light on this I'd be pleased to hear from you.
Cheers,
Blinky
Posted: Sat Sep 13, 2014 8:45 pm
by nab 301
Nothing helpful to offer on your query but I'm curious where the grub screw you mention is located?
Some fork stripping info here
viewtopic.php?t=12949&highlight=forks
and here
http://www.largiader.com/articles/sforks/
Lots of modified bits in this thread including radial caliper conversion (lots of work..)
viewtopic.php?t=7383&start=0
Posted: Sun Sep 14, 2014 5:44 am
by Blinky
Hi Nigel,
Thanks for the reply and the links. I had seen the first two but the last one on Kees' R1100S is really something. Man he went to some trouble!
I have found an Italian company that make the radial conversion. It is an entire fork foot replacement rather than a bolt on one like Kees was. It is hard to understand from them the attachment method though, hence why I'm doing my homework. From the images I have seen, I think they are threaded on. I'll know for sure when I take delivery of them.
The grub screw I referred to goes through the side of the fork foot on the wheel side at about caliper height as if to clamp on the tube. I can just see it on my bike if I look through the wheel at the opposide side fork foot and the MAX BMW fiche files refer to it as a M4x4 grub screw. If I can work out how to attach a photo I'll be able to show you.
Cheers,
Blinky
Posted: Sun Sep 14, 2014 6:25 am
by Blinky
Hi Nigel,
Grub screw is item 15 in the image below....
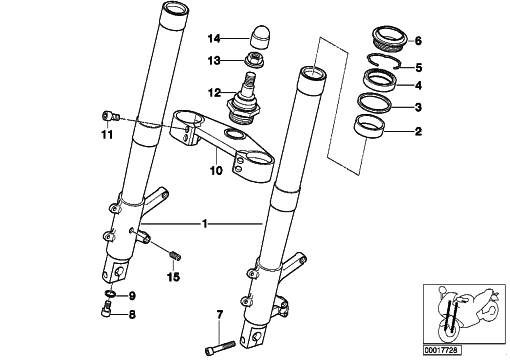
Posted: Sun Sep 14, 2014 7:25 am
by nab 301
Interesting ! I don't recall anyone over the years removing the fork bottoms.
Plenty have fitted upgraded discs and calipers .
Keep us informed if possible !
Posted: Sun Sep 14, 2014 10:00 am
by omg1010
There has been a kinda debate about this here in Germany. I recall one user here had been able to remove the fork bottoms with increadible difficulty. Apparently they are threaded (fine-pitch thread) and glued in place. Hence some serious heating and considerable force is required to take things apart. There are no instructions from BMW about how to do this and what torque is required ...
Hence I can only suggest trial and error. How to fix the fork-legs in order to apply the needed force is beyond my knowlegde.
Brgds
Oliver
Posted: Sun Sep 14, 2014 12:30 pm
by Blinky
Hi Nigel and Oliver,
Thanks for your responses. I'll keep you informed. Oliver, the picture below seems to align with what you were saying about a fine thread. I'll give it a go and advise of my success (or otherwise).
Regards,
Blinky
[img]
[img]http://i1295.photobucket.com/albums/b624/richardcurtis1/CA52693A-B2E4-48D2-A377-29F6ABF11FA4_zpssj1ul3x6.jpg[/img][/img]
Posted: Sun Sep 14, 2014 1:40 pm
by omg1010
Hey Blinky, awsome stuff!!!! Do you have a link to the source/manufacturer/seller? Contact details?
Brgds
Oliver
Posted: Sun Sep 14, 2014 4:12 pm
by omg1010
I think the hardest part will be to suitably clamp the fork legs in order to be able to apply the necessary force. Also heating up the fork legs will not be easy as aluminium is a good heat transmitter. Maybe with a blow-torch?
Brgds
Oliver
Posted: Sun Sep 14, 2014 5:30 pm
by Corvus
How about removing the "grip" by a slot down the existing bottom pieces. They'd be scrap obviously, but hey, who dares wins.
Shed version = hacksaw or cutting wheel on angle grinder
Professional version = slitting saw on milling machine, with careful measuring to prevent slitting male thread.
Just a thought!
Posted: Sun Sep 14, 2014 6:31 pm
by omg1010
That would be the brutal and destructible solution ... But obviously a solution.
Brgds
Oliver
Posted: Sun Sep 14, 2014 9:15 pm
by Corvus
omg1010 wrote:That would be the brutal and destructible solution ... But obviously a solution.
Brgds
Oliver

Posted: Mon Sep 15, 2014 2:20 am
by dave the german
How about forks in situ and a bar in place of the wheel axle with a bit of heat?
Posted: Mon Sep 15, 2014 6:09 am
by Corvus
dave the german wrote:How about forks in situ and a bar in place of the wheel axle with a bit of heat?
What would stop the upper section rotating?
The fact they're shown as one piece on the parts fische suggests they're not designed to be split. I imagine that, were it practical, the designer would prefer them homogenous? I imagine they're made initially separate to facilitate reasonably practical machining methods? Guessing.
Other thing to bear in mind, should one attempt to unscrew with long lever. Force at a distance = bending moment as well as torque. Bending fork sliders = very bad!

Posted: Mon Sep 15, 2014 6:23 am
by Corvus
Corvus wrote:dave the german wrote:How about forks in situ and a bar in place of the wheel axle with a bit of heat?
What would stop the upper section rotating?
.....
Apologies. The fork brace would. To a degree.
See my comments re bending!
A very long lever, poking our equally both sides would help cancel any bending moment. I wonder how well they're glued? Oxidisation in there won't help matters, I guess.
Cheers.